General manufacturing
We are working to help the manufacturing industry in Ireland to safeguard our precious water supply.
Water mapping
A water balance provides a full picture of every water-consuming component on site. It serves as the first step in uncovering opportunities for savings. We propose including all flows of water into and out of the six basic categories from the water balance format such as;
- Inlet water pre-treatment
- Cooling towers
- Boilers
- Processing (any water consuming facility which is a part of the production process)
- Wastewater plant (if it exists), or water effluent
- Other (ash ponds in a power plant)
Water related costs
In addition to capturing related flow capacities, collecting all related costs will provide an insight into where to save money on water bills. These are the following related costs:
- Water use
- Wastewater discharge fees
- Pre-treatment technology
- Energy costs associated with water use (heating, pumping, water treatment etc.)
- Regulatory costs (permits, compliance assessment, etc.)
- Costs for water management measures (staff time / resources, technology, equipment and materials)
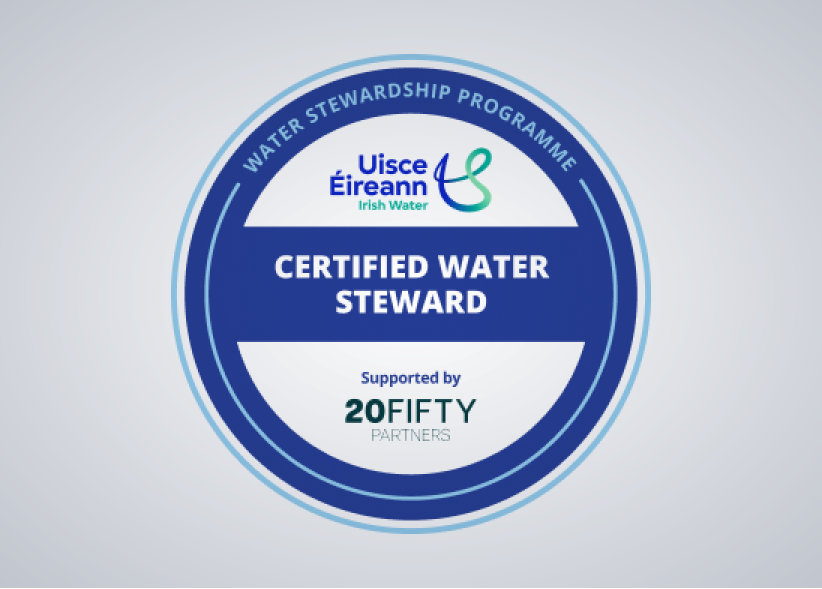
Water Stewardship Programme
Identify opportunities
Sources for Water Reuse and Recycling
Based on your water balance, rank the various components by water usage and focus on the largest water users. Identify leakages and sources for waste like excess cleaning and washing.
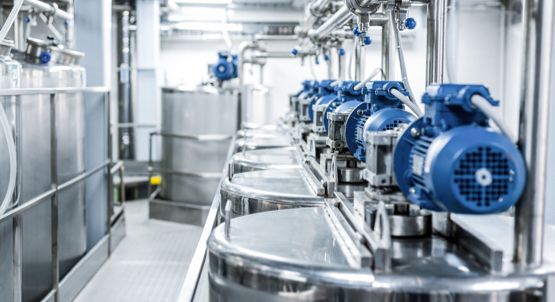
Equipment cooling
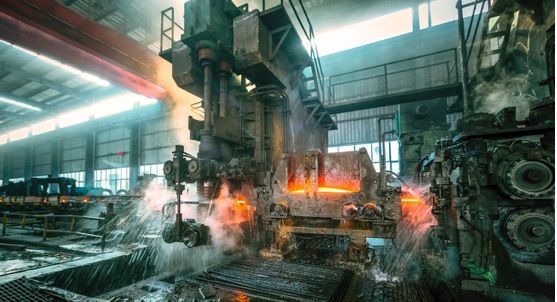
Equipment rinsing and cleaning
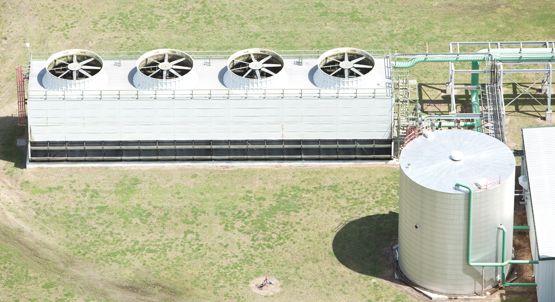
Cooling towers
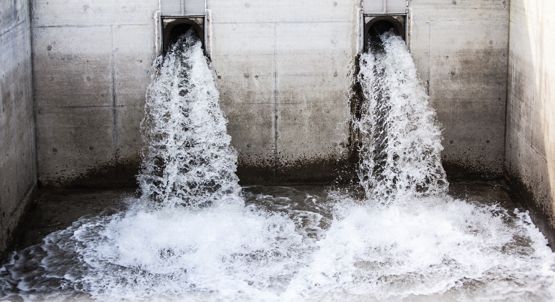
Alternative water sources
Engage stakeholders
Getting your stakeholders involved early on is essential in establishing initial buy-in, and ensuring the ongoing success of any water conservation campaign.
Your employees as a source for water savings ideas
- Survey your employee base by asking them to identify sources of waste. Employee awareness is a great way to uncover savings opportunities and to engage them in an execution program.
- Launch an employee awareness program. Provide them incentives and awards such as the most eco-friendly employee award, for being proactive in helping your company save water.
- Communicate with them on weekly basis - progress and success stories.
- Hold managers accountable for adopting ideas and executing them.
Develop strategy and action plan
- Identify process and product innovations and estimate the total effect on water savings to establish a goal.
- Establish a budget and procure funding. Outside funding and grants can be available - try Enterprise Ireland GreenPlus or GreenStart programmes.
- Develop a timeline for implementation and schedule periodic reviews with the water efficiency team to monitor progress.
- Develop an internal communications plan to continue engaging employees and creating awareness.